The Role Of Prototypes In The Product Design Process
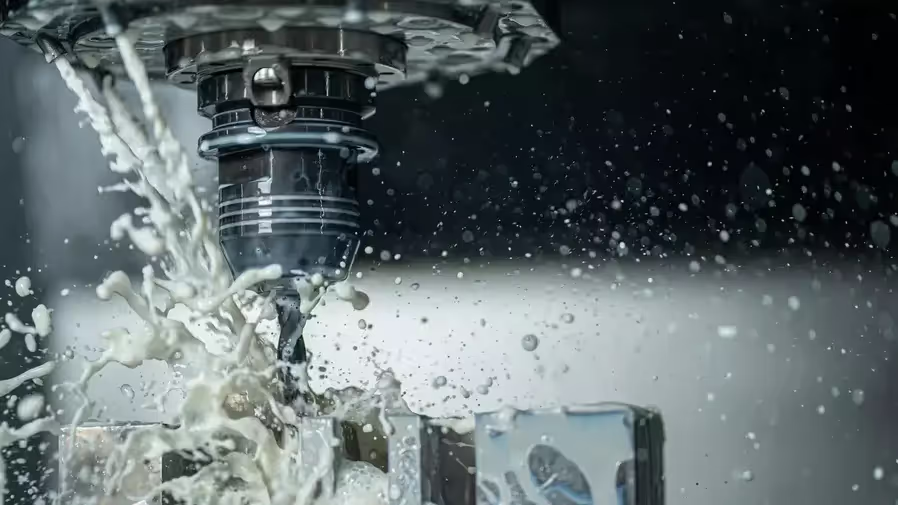
The Role Of Prototypes In The Product Design Process
With the growing popularity of digital product design and UX design the word prototypes is becoming synonymous with digital mock-ups and testing apps. The technological advancements in virtual prototyping are also providing a way to save time and effort in the prototyping stage which is becoming more commonly taken advantage of by novice designers over physical prototyping. While virtual prototyping offers undeniable advantages, which we will explore later, relying exclusively on the virtual approach will result in missing many important discoveries that would be uncovered through physical prototyping. In this blog we will explore the importance of physical prototyping and why it justifies the extra time and effort it requires as well as how to utilize virtual prototyping in an effective manner.
Firstly, what is a prototype? A prototype serves as a bridge between the designer’s imagination and the physical space. While there are many forms of prototypes of varying fidelities, essentially, they are physical mock-ups of a design, or portion of a design, which allow the form and functionality of the design to be assessed and developed in the physical space. Simple proof of concept prototypes can be enough to prove the fundamentals of the design. Higher fidelity presentation models showcase the end use materials and finishes as well as core functionality and mechanisms that contribute to the product working.
Virtual prototyping has a time and place, and when used inline with physical prototyping, it is a valuable tool which can save you time and money. Virtual prototyping is the process of using computer aided design (CAD) to test certain aspects of designs. CAD software’s allow the creation of precise 3D models that exhibit all the features and characteristics of the physical design in a virtual environment. These CAD models can be enhanced though rendering, which involves applying materials, textures and colours to the model as well as configuring environments, lighting, and cameras to create images of the design that closely resemble photographs of a physical product. Photorealistic renders are a useful tool in assessing the form of the design in 3D without needing a physical prototype. Functionality and how the product performs under various conditions can be assessed using Finite Element Analysis (FEA) simulation tools. FEA lets you run simulations of mechanisms and the application of simulated physical conditions to the design to see how it behaves. So, utilizing these virtual prototyping methods can identify any potential issues before committing to the significant costs of physical prototyping.
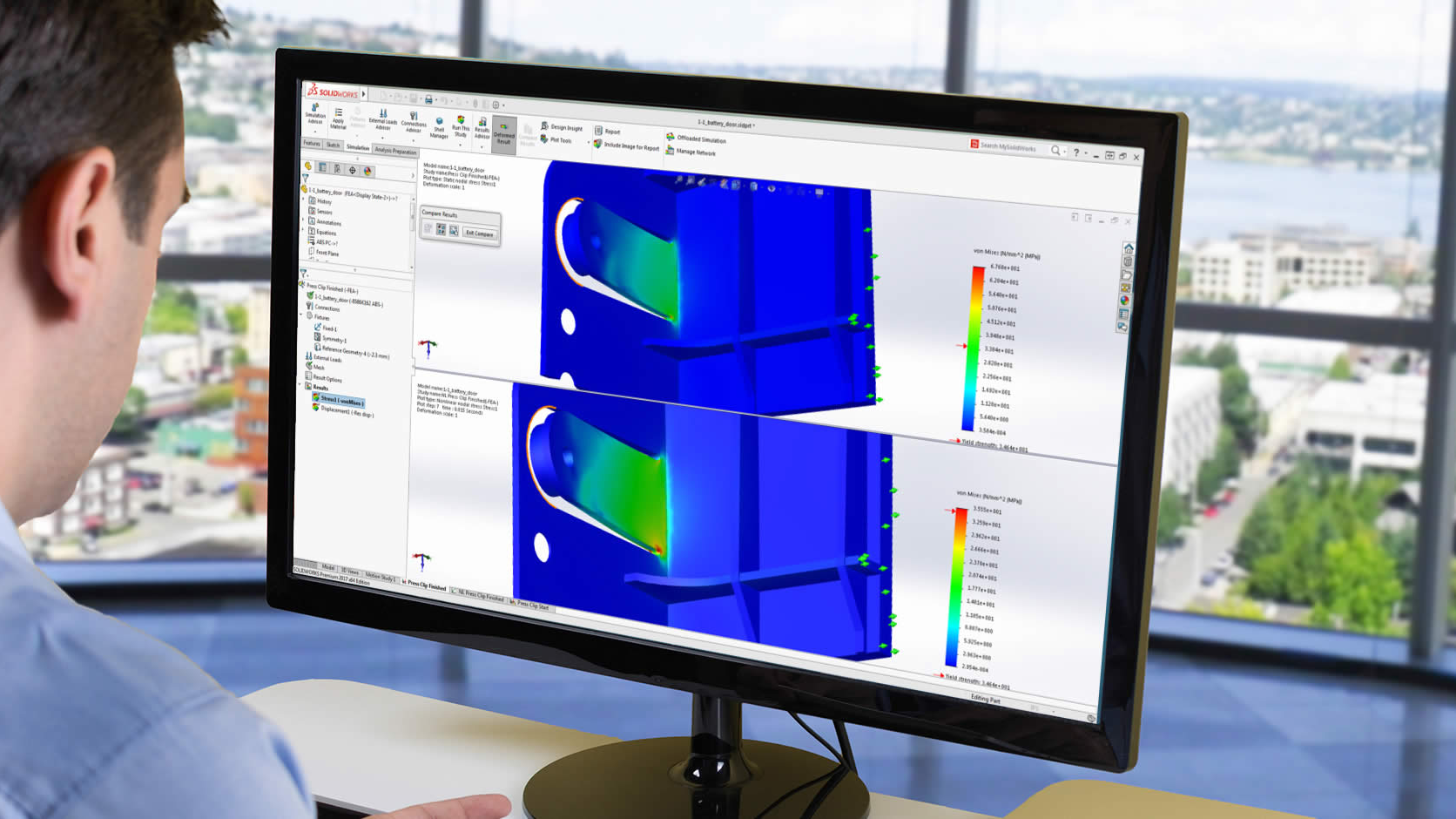
Benefits To Prototyping
Visualization and Communication
Prototypes have the ability to communicate ideas and virtual images in the physical space. Whilst sketches, CAD models and renders are a useful visualization tool, they can only show so much and can sometimes be hard to properly understand the 3D form and proportions. Physical prototypes, however, provide a 3D, physical form that can be held, manipulated, and understood. They communicate the design choices made and allow you to properly understand what they portray in the physical product. It’s a communication tool that allows you to effectively communicate the design to a wide variety of audiences, from target customers to investors
User-Centric Design
The importance of involving the user in the design process is critical if you want to achieve designs that properly meet the wants and needs of the user. Prototypes serve as a useful tool for assessing the designs usability and perception by the target market. Whether it’s testing the ergonomics of a hand tool, the usability of a medical device or comfort of a piece of wearable tech, by giving users a prototype to hold, use and look at, designers can gather useful observations and feedback from real users before they have committed to a final design. This user testing often uncovers useful insights that weren’t initially obvious from the research stage and so gives the designer time to develop and refine the design and ultimately results in a more intuitive and useable finished product.
Functional Testing
Prototypes can be vital for evaluating the functionally of a design. Designs don’t always function as intended and so creating functional prototypes serves a method for testing this before committing to expensive tool design and manufacture. First ideas can often be improved, so as well as just testing functionality, by experimenting with different materials, mechanisms and technologies in the physical space, prototypes almost always result in improvements to the end performance of the product. It also ensures the final product meets the intended performance standards as well as meeting any safety standards.
Iterative Refinement
The design process is not a one-way street, it’s iterative and involves continuously zooming in and out on the problem. Creating an intuitive product that works exactly as intended requires continuous development, multiple iterations, and improvement. Prototyping supports this by allowing designers to make incremental changes and developments based on real life feedback and test data.
Cost Savings
Early prototyping is normally a very cost-efficient way of testing designs, it can be as simple as carboard mockups, handmade foam models or 3D prints. Whilst higher fidelity prototypes can be more expensive, identifying and solving any design problems during the prototype stage is still far cheaper than making changes once production has started. This is where virtual prototyping can be a handy tool as utilizing virtual methods before moving on to high fidelity prototypes can result in fewer iterations of the higher fidelity prototypes being required. Think of prototypes as a safety net for catching potential issues before they turn into manufacture issues or recalls.
Aesthetic Evaluation
Prototypes don’t only serve as a tool for assessing functionality but also present a method for judging the aesthetics. An attractive product catches the eye of the consumer and helps it to stand out on the market. Prototypes allow you to assess the visual aspects of the design, such as colour, form and material. Whilst CAD renders can give you a good idea of these things, seeing the design in the physical space allows you to see the design how the end user will see it and will give you a more accurate evaluation of its aesthetics. This is a useful way of ensuring that the design looks as good as it functions and checking the aesthetics trigger an emotional response in the user.
Material Selection
Materials have a big influence on a products performance, durability, and aesthetics. Building prototypes from a number of different materials means you can assess their suitability. Physical experimentation allows designers to make a decision on material selection based of real findings rather than assumptions and ensures that the materials used are appropriate for the products intended use.
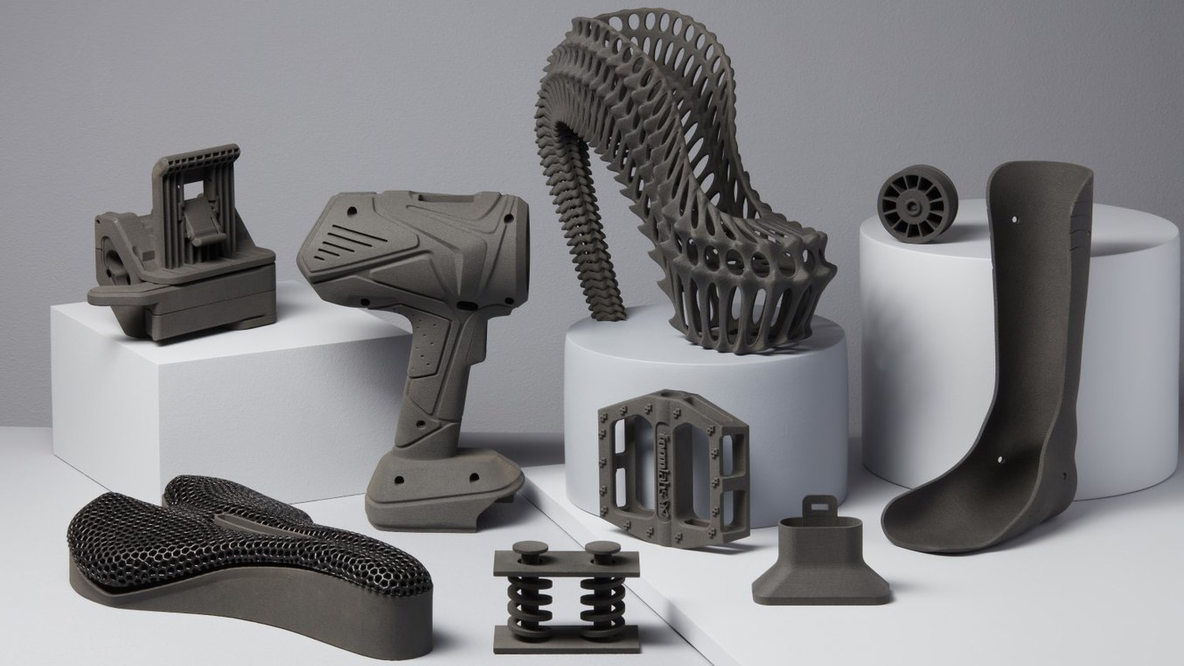
In the product design process, prototypes are an invaluable tool for creating innovative products that function as intended and have the aesthetics to stand out on the market. They allow designers to see their designs in the physical space, gain user feedback and refine product functionality, informing their design decisions so that assumptions do not have to be made. But arguably most importantly, they save time and money by preventing the need for changes once production has already begun.
We provide businesses with product design consultancy, industrial design, prototype design & related services.